The Impressions Long Beach Expo took place from January 20 to 22 in Long Beach, California and gave our Decorator and Digital Solutions Team a glimpse into what’s trending in our industry. Here’s a few quick highlights.
- Direct To Film continues to grow, with even more equipment on display than we saw at Printing United in October.
- Heat Transfer technology shows no signs of slowing down, as it continues to gain traction in ingenuity and application.
- Speed is the name of the game within digital technology as competing industry players look to simplify DTG output with amazing efficiency.
- The phrase “On-Demand” was being said everywhere we turned.
Most importantly, sustainability efforts are proudly on display in our industry, from eco-friendly reclaiming agents, to recirculated water in automated screen room equipment, and a surprising development from a company seeking to encourage us to rethink the age-old classic technique of embroidery.
Let’s take a deeper dive into what we saw at the show.
Coloreel Brings a Sustainable, On-Demand Thread Technology to Embroidery
Early embroidery can be traced back to 30,000 B.C, which is astonishing to think about when we consider how fundamentally prevalent it is to our industry. While recent innovations within the medium such as automatic thread tension adjustment and fabric thickness detection are important steps forward, the world of embroidery remains largely unshaken by its consistent process and protocol.
Coloreel has entered the chat to bring forward a new technology that completely upends how we approach the consumable aspect of embroidery: the thread itself.
At its core, Coloreel serves as a sustainable production efficiency technology. Instead of requiring a production space to be invested in hundreds of varying cones of color, Coloreel asks that you simply invest in a single reel of clear recycled polyester thread.
This simple ask is realized by introducing a revolutionary unit that instantly colors thread on-demand.
This single reel of thread sits at the back of the Coloreel unit and is fed through the Coloreel color process chamber where it undergoes colorization, fixation, washing and lubrication. The completed thread exits the Coloreel unit and is then embroidered with any type of industrial embroidery equipment.
The use of Coloreel eliminates various forms of waste, including water, thread, and chemical usage throughout the industrial thread dyeing process.
Perhaps most conveniently, an operator can utilize their favorite software for the stitch design, and it will work in conjunction with Coloreel’s technology. Coloreel also offers a colorization studio software in which you can add colors and design effects (such as smooth color shifting and gradients) amidst a robust color palette for free. The operator can then use their digitized file alongside the color design file to produce the finished Coloreel product.
Our industry continues to be awash in a sea change of innovation that promotes sustainability and on-demand capabilities. While the world of Digital Printing continues to advance and evolve, Coloreel has brought forward a truly thought provoking and enticing advancement to the ancient world of embroidery.
The Stampinator Gets a Seal of Approval
While universally capable of affixing to industry automatic screen print presses, Slant Engineering had their innovative Stampinator on display in the ROQ booth at Impressions Long Beach.
The Stampinator serves as an extremely innovative piece of accessory equipment that accomplishes multiple functions while attached to the front and rear screen clamps on a single station of an automatic press. It sits over the platen, like a flash unit, and essentially serves as an in-head combination heat press/flash cure/fabric press.
The Stampinator can automate the process of heat application for transfers, such as foil, vinyl, rhinestones, Direct to Film, and other heat-applied graphics as the garment makes its way around the carousel.
In addition, like a hot-iron fabric press or smoothing roller, the Stampinator can matte down fibers as a part of the pre-print process. This can assist in building a solid foundation for the underbase while combating fibrillation and reducing the ink deposit that is needed.
If using as a flash cure for screen printing, the Stampinator can flash an underbase in 3 seconds or less at a controlled temperature, replacing a standard quartz or infrared flash.
Lastly, while on the topic of curing, the Stampinator can theoretically replace a conventional conveyor dryer if desired. By placing the Stampinator in the last head of the press, you can contact cure on-press and immediately remove and load the cured shirt to stage it for finishing services.
If operating a big enough press, the ability to incorporate multiple Stampinators into the workflow exists to assist both the pre-print and post-print process of production. Meanwhile, if you would like to automate your heat transfer output, few other options outside of the Stampinator exist today.
In the Stampinator, Slant Engineering has built a piece of screen-printing ingenuity that perfectly encapsulates why attending these industry shows is so important.
East West Machines Innovates with a Carousel Heat Press
As unique Heat Transfer and Direct to Film technology continue to drive everyday conversation within our industry, the opportunities to automate the application process appear to be increasing.
Introducing the Four Station Automatic Carousel Heat Press (EW-HP4A) from East West Machines. The EW-HP4A is East West Machine’s flagship model and was built with the goal of creating the highest capacity heat transfer machine in the market today.
Featuring four stations, this automatic heat press includes four platens, a 16” x 20” heat element (press) and can press over 360 heat transfers per hour. Included with a purchase comes a set of four 6” x 6” pallets to accommodate smaller print areas, or substrates such as koozies, and a set of four 16” x 20” pallets for full chest and full back decoration. The machine is capable for use on apparel, paper, hard and soft goods, packaging, signs, sublimation and more.
With four available stations, an operator can load the garment at the first station and control the index automatically or semi-automatically by virtue of the foot pedal control. Station two can serve as a transfer placement station, while station three features the fully automatic heat element, and station four completes the job with a place to unload. The machine can also be entirely run, start to finish, by a single operator.
With automation in mind, East West Machines has brought forward a piece of equipment to supercharge a shop’s transfer production.
Brother’s Smart Platen Technology Brings Efficiency to their Digital Line
High volume print shops have a new, fully automated DTG system to consider when looking to output digital work at blazing speeds. Brother’s Digital Line (DL2200) can assist in controlling an on-demand shop’s labor costs while customizing every shirt that’s printed with their new all-in-one system.
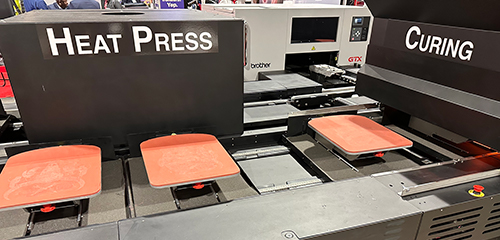
This system allows a single operator to manage the entire DTG process utilizing a load station interface in conjunction with Brother’s Smart Platen belt transport to send each platen to the next available printer to eliminate production jams and increase output.
The shirt starts off by making its way into an Inline Pretreat with a triple spray width and dual pretreat fluids. It then immediately navigates into a pretreat curing box complete with thermal camera to optimize settings per each garment. The shirt then wraps up pre-production when encountering an inline heat press with adjustable pressure and time per garment thickness. This will smooth the garment fibers down in preparation for printing.
By inserting two Brother GTX600 units side-by-side on the carousel, the Smart Platen technology can then identify which unit remains available, thereby moving into said unit for production while the other printer completes it’s job. This creates an efficient production workflow and eliminates delays, as the prepped tee does not have to wait for production to complete.
The garments conclude their journey by being cured in an inline Firefly dryer, featuring the same thermal cameras found in the pretreat cure box. Brother has brought forward another great solution to the on-demand digital space with their Digital Line.
Image Technology Simplifies Custom Ink Mixing
Screen print shops are often tasked with two expectations when it comes to ink consumption and custom Pantone mixing: Dedicate a significant amount of floor space to an ever-expanding library of colors, and carefully weigh and mix a range of various color combinations to achieve a specific custom pantone.
For most shops, this process is not too burdensome. However, as shops grow in scale and volume, the demand for this process can become time-consuming and tedious. For these large-scale shops, Image Technology has created a custom Pantone ink dispensing machine called the Speedy Mix Color Pro 1, that can simplify this process by reducing the number of required steps down to the push of just several buttons into a Programmable Logic Controller (PLC).
This PLC is included alongside a monitor, keyboard, mouse, scale, and stainless-steel work bench. By simply entering in the desired pantone, the Speedy Mix Color Pro 1 pneumatically pulls from up to 16 pails of various pigments around its work bench and delivers an automated custom Pantone for pints, quarts, gallons and can be configured for up to five-gallon containers.
The magic all comes from Image Technology’s Cloud Color Matching Software, which offers precise and dependable results in the dispensing of pigments for ready-to-use colors. This efficient use of ink decreases waste and creates less press downtime by delivering the perfect color during every sequence and can help create and expand a production facilities database of formulas without dedicating that floor space to the aforementioned library of ink colors.
Happy Decorating!
This was just a small sampling of what our team found while walking the floor of Impressions Long Beach. Many other intriguing developments are taking place throughout our industry, and we will be happy to share more information about them as the weeks and months of 2023 go on.
Until then, we hope to see you at your nearest Decorator Show sometime this year. Feel free to consult the Decorator and Digital Solutions Team landing page for a complete list of our Team’s 2023 show attendance.