In the early days of September, the Printing United Expo returned to Las Vegas, bringing with it an exhaustive amount of content, stories, announcements and education. The SanMar Decorator Solutions Team was on-hand to capture the big stories that caught our attention.
- The Latest in Direct To Film
- ROQ Enhances Heat Transfer Efficiencies
- A New Competitor in DTG
- Standout Embroidery from Tajima
- M&R Adds Screen Printing Automation
Direct to Film Continues to Evolve
Direct to Film (DTF) has grown across the industry over the last three years, and as we saw at Printing United, that’s not slowing down. There was plenty of DTF technology to evaluate, and our team took note of several new and upcoming units.
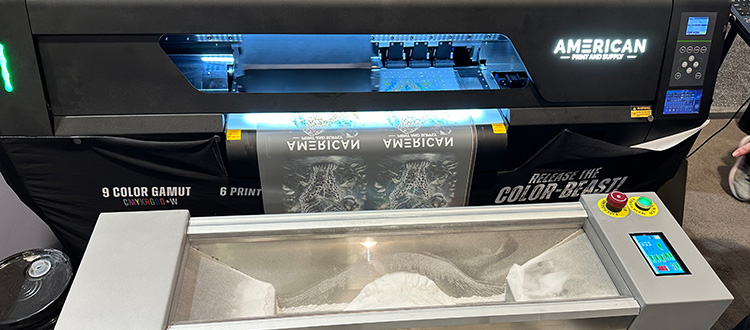
Peoria-based company American Print and Supply unveiled the Hydra, their latest DTF system.
The Hydra identifies itself as the next generation of DTF printing, boasting six print heads and an expanded 9-color gamut (CMYK, RGB, White, Orange). It’s a unique approach to the traditional CMYK/W print head technology dominating the market today.
One of the largest drawbacks many decorators cite with Direct to Film is the technology’s inability to match Pantone colors. This can be problematic when working with businesses or organizations that require an exact Pantone match to adhere with brand standards. This new 9-color gamut technology could be the closest a piece of DTF equipment has ever gotten.
The Hydra advertises an ability to print 275+ sq. ft./hour (3 rolls of film per day) with up to 450,000 color gamuts achievable.
American Print and Supply’s Hydra is coming soon.
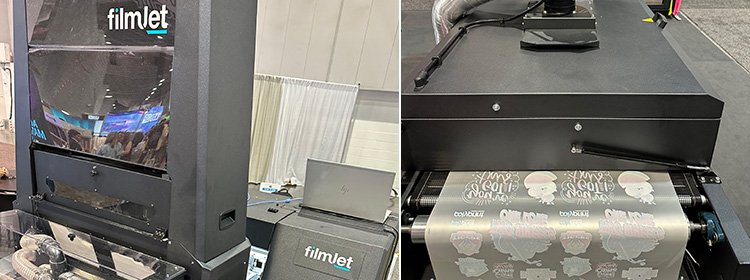
PolyPrint, from the EU, was showcasing its first all-in-one DTF system: the Filmjet. This is a high-efficiency system that delivers longer unattended print runs and minimizes the need for human intervention.
While the Filmjet integrates automation technology, industrial-grade printing speeds, smart system control and constant film tension, one of its standout features is the auto powder-recycling component.
The majority of automated DTF equipment requires a staff member to monitor and reload the adhesive powder applicator as it nears depletion. The Filmjet utilizes an air knife to force excess powder off the film carrier, where it’s vacuumed up through a port and added back into the existing powder stock. An antistatic bar neutralizes static electricity on the film to prevent powder adherence and maintain cleanliness.
The FilmJet includes automatic white ink circulation and CMYK ink agitation. For those decorators looking to step into the next phase of printing velocity and efficiency, or those interested in becoming transfer resellers, the Filmjet is worth a hard look.
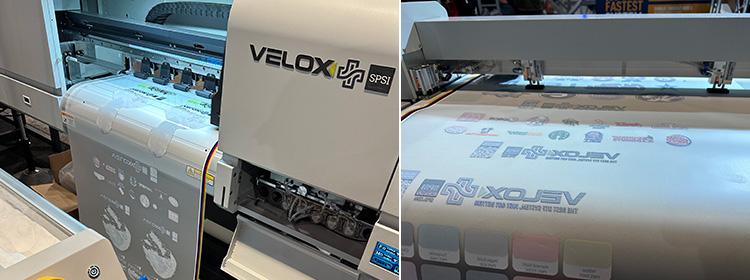
SPSI, a company based out of Minnesota, was on the floor to show off the Velox Plus.
This second generation of SPSI’s Velox system brings several enhancements, including an ability to adjust the configuration from a 3-head printer to an ultra-fast 5-head printer. The 3-head configuration allows for 60 linear feet per hour. While some shops may find this wholly sufficient, SPSI can convert the same printer into 5 printheads, which will boost the capability of the system to 120 linear feet per hour.
Velox Plus is capable of printing up to 26” rolls with a built-in air purifier, automatic ink recirculation, and updated Wasatch Rip Software that is capable of pairing with their new NuCut F6090 Automatic Cutter.
The NuCut adds another layer of efficiency and precision to the Velox system. This equipment integrates a camera to read QR codes on the film for precise cutting, creating accurate results without manual intervention. Being able to create cut files directly on the Velox with Wasatch Rip Software streamlines the workflow by reducing the time and effort required to prepare prints for cutting. Added flexibility allows the NuCut to cut around individual prints set up in standard 16” x 20” or even cut out individual gang sheets.

ROQ Feed Complements the ROQ Impress
The ROQ Impress was unveiled in Atlanta last year, as you may have seen in our Printing United 2023 article. This automated carousel proved to be ROQ’s first foray into efficient heat transfer application.
One year later, and ROQ has continued to support this equipment with the ROQ Feed, an ancillary piece of equipment that automatically places the transfer on each garment, eliminating a step in the production process and reducing the number of operators needed on the equipment.
Manual transfer placement is eliminated, as the ROQ Feed introduces a built-in control that can be adjusted for the Y-axis placement of the transfer, ensuring perfect alignment. For fine adjustments, the X-axis manual adjustment feature allows the user to easily achieve the desired placement, reducing human intervention and lowering production costs.
Transfer sizes of 15cm x 15cm up to 40cm x 50cm can be accommodated via the adjustable transfer tray, with smaller sizes available upon request. A central suction cup handles smaller transfers, while four suction cups transport larger transfers for full chest or full back prints. These small suction cups are one of the very few consumable elements in the machine’s operation.
Finally, you can set and establish recipes for specific jobs based on the consumable used, so recalling a previous order is as simple as a few touches of the control pad.
ROQ plans to unleash more automated equipment for the ROQ Impress in the near future, and we’re very excited to see just how automated this machine can get.
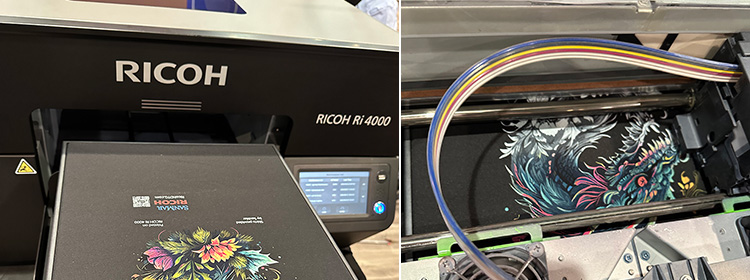
The RICOH Ri 4000: DTG Strikes Back
Not to be outdone by DTF, Direct to Garment (DTG) had some substantial updates on the floor this year, including the RICOH Ri 4000, a new competitor within the tiny but mighty 100% Polyester DTG printing market.
This technology utilizes a built-in Enhancer, which means an end to manual pretreatment. The printer will automatically complete the pretreat process before printing by way of the system’s inkjet heads. Also of note is this printer’s ability to utilize less pretreat material, as it only applies this Enhancer to the print area instead of the whole surface. This reduces waste and eliminates the “pretreat box” that is often undesirable for both production departments and end users.
RICOH’s newly developed ink can now print on 100% Polyester garments, as well as cotton and blends, and is built for speed and efficiency. By bringing this all-in-one, multi-fabric friendly process into a tabletop vessel, RICOH has found a way to dramatically reduce costs compared to their competitors.
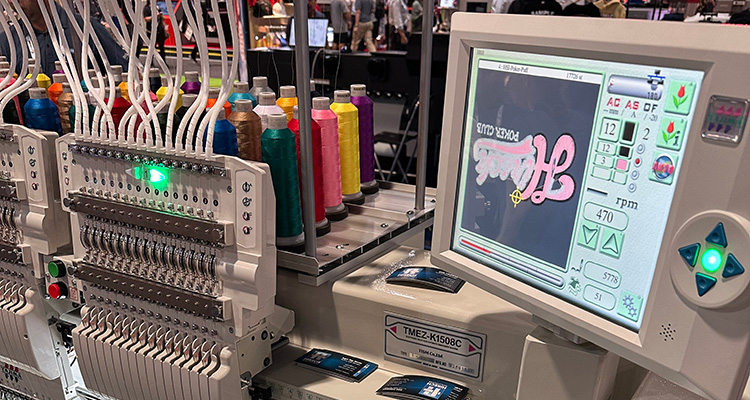
Tajima TMEZ-KC Equipment Stands Out
A somewhat limited supply of Embroidery equipment on the show floor this year allowed what was on display to really stand out. This included the Tajima TMEZ-KC series, which was featured in the Hirsch Solutions booth.
This flagship model from Tajima brings multiple enhancements and features to the tried-and-true world of embroidery.
The newly designed Slim Cylinder Bed has a 12% decrease in diameter compared to conventional cylinder models. This widens the range of applications to cover tubular products like sleeves and pockets. The Wide Cap Frame has also been redesigned and allows enhanced stability of the substrate while increasing the rotational speed to 1,000 rpm.
The Digital Compressor Foot can be set to the thickness of the fabric, so it does not overpress the material and cause shadows or damage. By optimizing the timing of the press, this can suppress fluttering of the embroidery material, which results in a consistent application throughout production. The presser foot is effective for hard-to-decorate materials like high-stretch and thicker fabrics, as well as leather.
Additional performance-enhancing features include a reinforced tubular frame arm, reinforced upper thread lock and an upgrade to the main shaft motor.
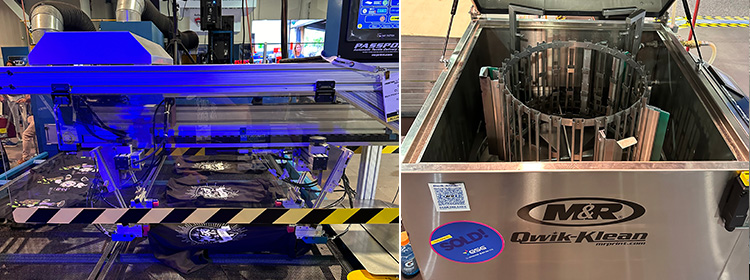
M&R Emphasizes Efficiency
With a vast assortment of equipment on display, M&R’s booth was loaded with screen print and digital technology. From their Gauntlet 4 to the Quatro DTF System, there was no shortage of product to discover.
Two particular pieces of equipment M&R had on hand highlighted efficiencies within the shop ecosystem.
The M&R Passport Automatic T-Shirt Unloader has been around for many years, but never fails to amaze. The Passport was the first automatic unloader to remove a textile quickly, carefully and consistently from an automatic press. This machine lowers labor costs by reducing the number of people needed on-press. It doesn’t tire or lose concentration, and it maintains consistency throughout its operation.
This patented equipment also minimizes design distortion by gripping the substrate with four patented grippers on retracting arms and lifting it straight up off the pallet. The substrate is then deposited onto the conveyor dryer belt for curing.
Best of all, the Passport works with all M&R automatic presses and supports platen sizes between 10” x 10” and 24” x 30”.
Also on display was the M&R Qwik-Klean Self-Contained Automatic Squeegee and Floodbar Cleaner.
Cleaning equipment is often one of the least desirable jobs in a print shop. So, M&R has added another piece of automated equipment that vastly reduces a highly labor-intensive and tedious process.
Through a combination of a high-volume spray and a rotating squeegee/floodbar holder within a single chamber, the Qwik-Klean can clean 24 pieces per cycle. Under optimal conditions, this equipment can run three cycles per hour, averaging 72 pieces per hour of a clean squeegee/floodbar combo with adequate ink scraping prior to cleaning.
The Qwik-Klean also reduces environmental impact and reduces operating costs by recirculating the cleaning chemicals within the chamber.
See You in Orlando!
The Printing United Expo shifts to the Orange County Convention Center in Orlando, Fla., from October 22 to 24, 2025. We hope to see you there! Even if we don’t, you can count on our Decorator Solutions Team to keep you caught up on big stories from the Expo floor.
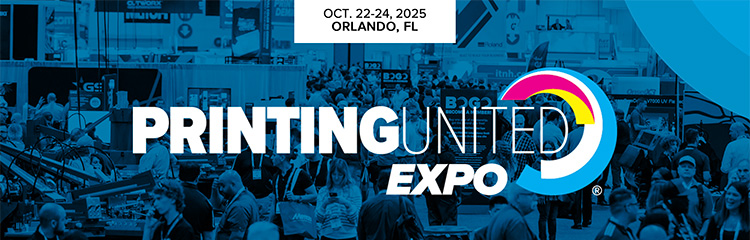