A constant question every screen printer has to weigh is whether or not the ink has cured correctly. The results of the ink being either under- or overcured will be a print that doesn’t hold up to the test of time in a washer. There are inherently unique differences to printing with water-based and plastisol inks. Since each process is different, we’ll cover each in different articles. For today, let’s work through some common practices and issues that may arise while placing plastisol ink on a garment.
As decorators, the risk of undercuring a garment leads many to baking the ink so long or hot that a cured finish is the only possible outcome. There’s always a risk, especially when using a flash, for an undercured print. Flashes are designed to stabilize a base layer just enough for a top layer to be applied. As the garment is run through the dryer, the belt length and tunnel temperature provide enough heat over time to penetrate all layers for a final cure. If the time under heat isn’t long enough, the base layer may not cure completely. The print likely will pass a stretch test, but you may see cracking or dye migration once washed.
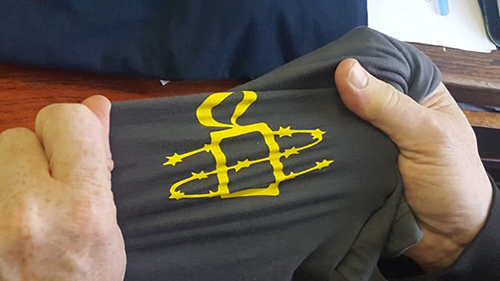
While checking temperatures, remember that a heat gun is checking the garment and/or ink surface temperature. Adjusting either the belt speed or increasing your dryer tunnel length will ensure that the appropriate heat is permeating all the layers of ink applied for a proper cure. What if your belt or tunnel length isn’t the desired length? What will happen if you provide too much heat, if even for a short period?
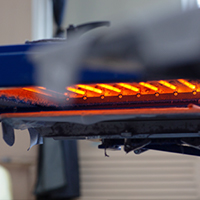
You should first check if the garment itself requires a lower-cure ink. Any blend with a synthetic filament usually should have an ink that allows for 300 degrees Fahrenheit or lower. Most inks have a safety range that the manufacturer can provide to appropriately cure their ink. So, if you find the length in tunnel may not be enough causing higher temperatures and/or using heat sensitive garments, then reach out to your ink supplier! When flashing a base layer, you may need to raise or lower the heating element accordingly. Generally, you’ll find the separation from the garment to be 2-3 inches for 6-9 seconds on cotton and 2-3 seconds on 100% polyester/synthetic filaments.
It is possible to overcure the ink as well. The print itself often will look as expected until laundered, then after several washes you’ll typically see the the ink start to crack and fade prematurely. Too much heat, including off the end of the dryer, can have results including ghosting if using a catch basin, discoloration of synthetic fibers and dye migration. It is highly recommended to internally wash test samples, especially on larger runs, to ensure the process is providing the desired results.
An often-overlooked component is the time of year and the environment of your building. Variables to pay attention to include heavier moisture content (humidity), hotter summers versus colder winter days and early morning versus mid-day printing. As you start your mornings, always make sure to warm up the flash unit, your dryer and belt, the pallets on press, potentially a quick run of the garments down the belt themselves prior to adding ink and even a quick stir of your ink.
While using plastisol ink can seem relatively bulletproof, the world of decoration is a constant exercise in science. Always remember to test, test again, and if any doubt is lingering, test once more!